People with diabetes rely on insulin pumps 24/7—any power fluctuation can threaten their health and safety. For manufacturers, this means one thing: the power adapter must never fail.
Insulin pumps require power adapters with high stability because even minor voltage fluctuations can interrupt insulin delivery, risking under-dosing or overdosing. A stable power adapter ensures safe, continuous pump operation.
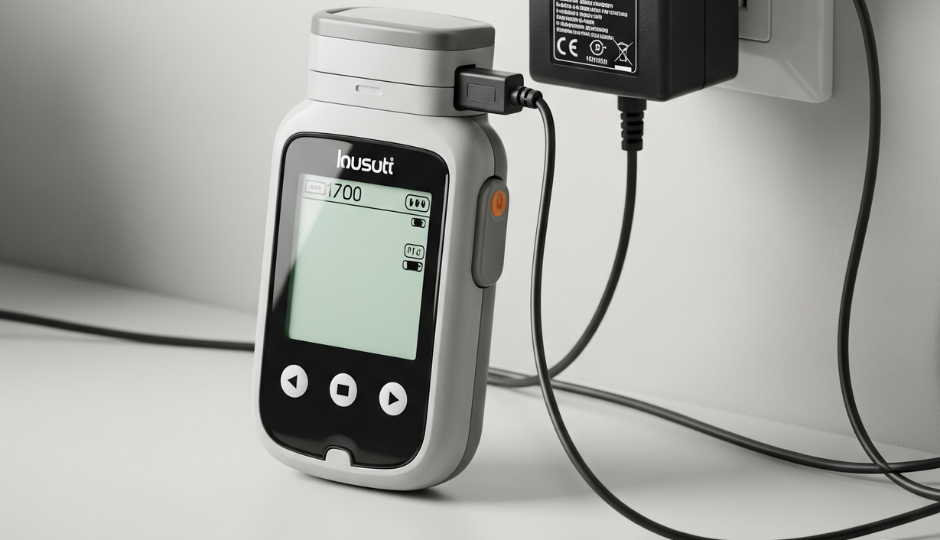
If you’re developing an insulin pump, the last thing you want is a power failure. The pump may look compact and low-power, but it’s a life-sustaining device that requires precise, continuous delivery. A cheap or poorly regulated adapter can damage components, introduce noise to the control circuitry, or worse, halt insulin flow. In this article, I’ll break down why a highly stable power adapter isn’t optional—it’s essential.
What Happens If an Insulin Pump Gets Unstable Power?
A voltage drop or spike may sound harmless, but for medical devices, it can mean the difference between life and death.
If an insulin pump receives unstable power, it can miscalculate insulin dosage, overheat, or shut down. This may result in serious health complications or emergency hospitalization for the patient.
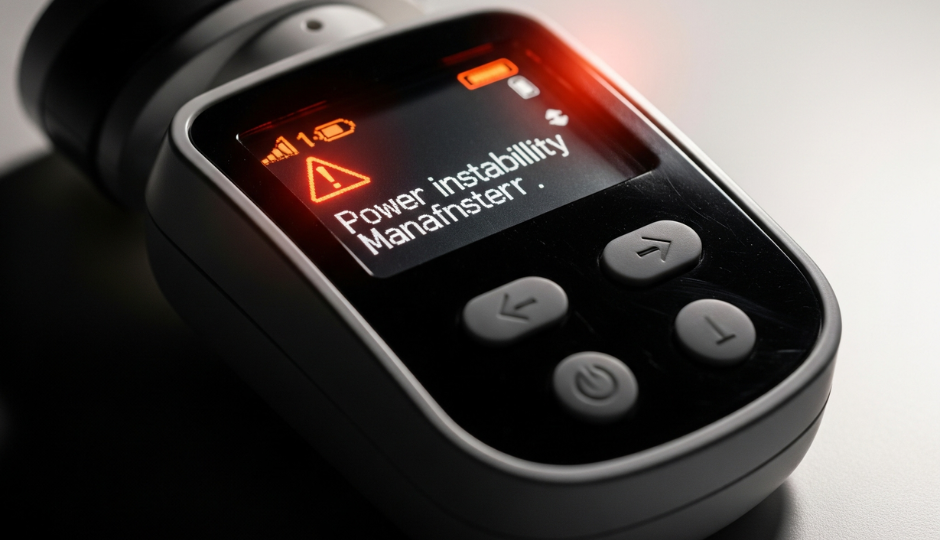
Power instability doesn’t just cause inconvenience. For insulin pumps, it can directly affect how much insulin is delivered. If the voltage falls below the operating threshold, the motor may stall, delaying insulin release. If voltage spikes, it can damage the control system or cause sudden insulin bursts. Patients may experience hypoglycemia or hyperglycemia, both of which carry serious risks.
Key Power Risks for Insulin Pumps
Power Issue | Potential Outcome |
---|---|
Voltage Drop | Interrupted delivery, device shutdown |
Voltage Spike | Internal damage, safety malfunction |
Ripple/Noise | Signal distortion, motor error |
Overcurrent | Component overheating, short circuit |
Poor Efficiency | Battery overheating, shorter lifespan |
That’s why, when I select power adapters for clients in the medical device industry, I look beyond the usual voltage and current specs. I prioritize ripple control, voltage regulation, thermal stability, and medical-grade certifications like IEC 60601.
Why Are Medical Certifications So Important?
You can’t cut corners when people’s lives are on the line. Medical-grade compliance isn’t just a label—it’s a safety promise.
Medical-grade power adapters meet strict standards for leakage current, isolation, EMC, and reliability. These ensure the adapter won’t harm the patient or disrupt sensitive medical electronics.
Let me explain what these certifications mean in real life. For instance, IEC 60601-1 sets the benchmark for medical safety. It requires the adapter to have reinforced insulation, limited touch current, and a high dielectric withstand rating. This prevents electric shocks, even if the adapter casing is damaged or exposed.
For insulin pumps, the power adapter may touch the patient directly or indirectly. A compliant adapter ensures leakage current stays under 100 µA—far below the dangerous threshold. It also controls electromagnetic interference (EMI), which could affect nearby diagnostic devices like glucose meters.
Key Standards to Look for:
Standard | What It Ensures |
---|---|
IEC 60601-1 | Patient protection, leakage control |
IEC 60601-1-2 | EMC immunity and emissions |
UL 94V-0 | Fire-retardant plastic enclosure |
DOE VI / CoC V5 | Energy efficiency, less heat |
Without these certifications, no reputable medical company will accept your power adapter—even if it technically “works.”
How Do You Design for Long-Term Stability?
Designing a power adapter for a medical device takes more than selecting the right ICs. It starts with understanding how patients use the device in real life.
Long-term stability requires strict component selection, temperature control, and protection design, so that the adapter performs consistently over years of daily use.
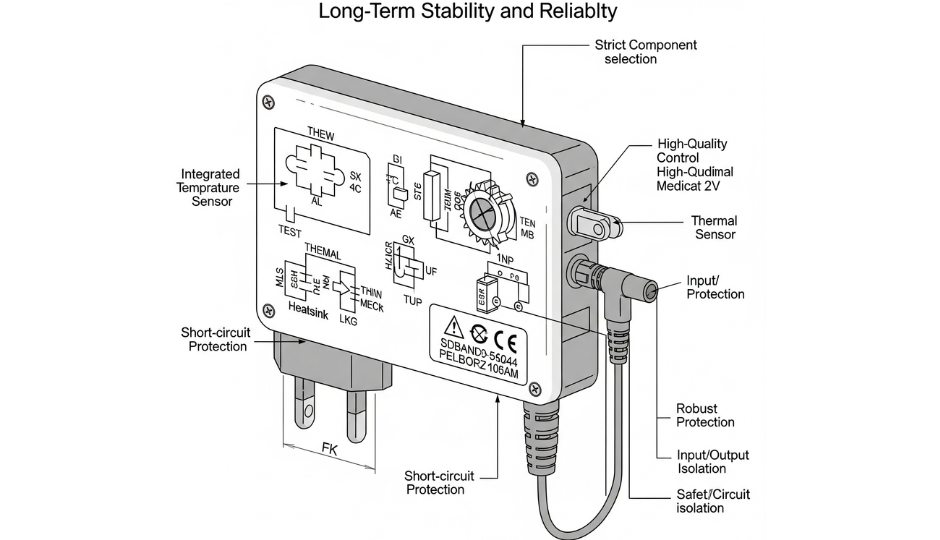
From what I’ve seen, insulin pump manufacturers need adapters that work in varied environments—hot, cold, humid, or dry. These adapters may be used by elderly patients or children. They’re often plugged in and forgotten. This puts pressure on the internal design to hold up for years with no failure.
Here’s what we focus on in our engineering process:
Design Factors for Stability
1. High-Quality Capacitors
Cheap caps degrade over time, causing ripple and dropout. We use low ESR, high-temp capacitors rated for 10,000 hours or more.
2. Thermal Control
We conduct derating analysis to make sure components don’t exceed 70% of their rated limits under continuous operation. We also use flame-retardant casing and thermal fusing for fire safety.
3. Built-In Protections
We design in OVP (overvoltage protection), SCP (short-circuit protection), and OCP (overcurrent protection). If anything goes wrong, the adapter shuts down instead of frying the pump.
4. Aging & Burn-In Tests
Before shipment, every adapter batch undergoes 100% burn-in testing at elevated temperatures. That way, early failures don’t make it to the end user.
This kind of overengineering may seem excessive. But in the medical field, it’s the only way to ensure peace of mind.
What Makes a Power Adapter Truly “Medical-Grade”?
Many companies claim “medical-grade” without passing the tests. So, how can you tell the difference?
A true medical-grade adapter not only has certifications but also demonstrates high MTBF, low EMI, and patient-safe isolation. It’s built for healthcare, not just labeled for it.
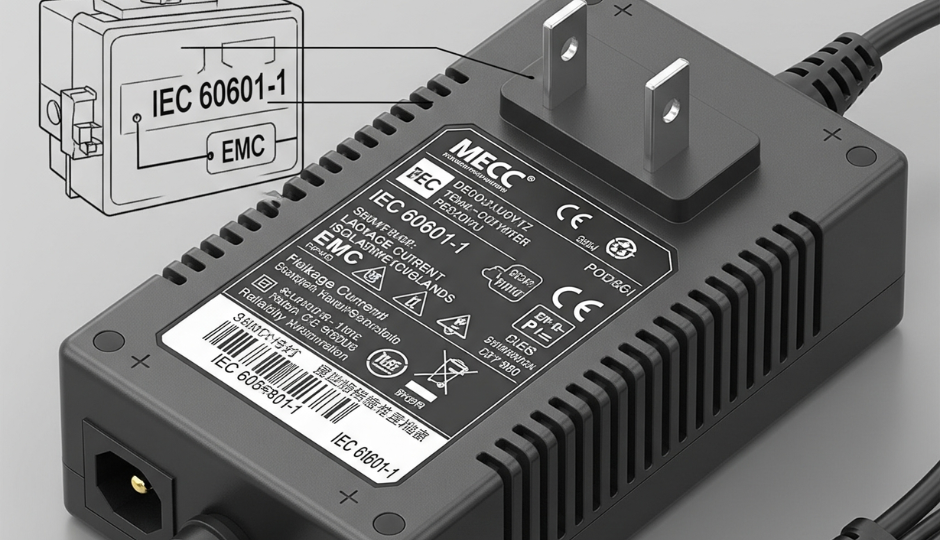
I often get asked this question: “Can we use a consumer-grade 12V adapter if it fits the specs?” My answer is always no, especially not for insulin pumps. Medical-grade power supplies are made with stricter design margins, redundant safety measures, and rigorous documentation. They go through production line testing that consumer units don’t.
Here’s a simple checklist I use when qualifying a “true” medical-grade adapter:
Medical Adapter Checklist
Feature | Why It Matters |
---|---|
IEC 60601-1 Certification | Protects patients from electric shock |
Reinforced Isolation | Prevents leakage from AC input |
2x MOPP Safety | Means of Patient Protection—double layers |
EMI Filtering | Reduces interference in clinical settings |
High MTBF (100,000 hrs+) | Ensures long-term reliability |
If an adapter doesn’t meet all these, I don’t even consider it for use with insulin pumps. Patients deserve better.
Conclusion
Power stability is not a luxury for insulin pumps—it’s a life-critical necessity. Only high-grade, medically certified adapters can meet the challenge.